L’enjeu
Lors de mon année de seconde, j’ai rencontré celui qui deviendra l’un de mes plus proches amis. Dès le début, nous avons développé un goût prononcé des débats en tout genre tournant autour de sujets aussi divers que les nouvelles technologies, l’économie, les sociétés modernes, les énergies ou bien les transports. Au cours de nos tergiversations, nous nous sommes rendu compte qu’une technologie avait un potentiel phénoménal et était fortement sous-utilisée et sous-estimée : l’hydrogène. Il est l’atome le plus élémentaire dans l’univers, base de l’arme la plus mortelle que l’Homme ait inventée. Et pourtant, il est également un formidable outil à notre disposition. Nous sommes alors en 2014. Le grand public parle peu des technologies entourant l’hydrogène. Nous décidons alors de nous renseigner davantage ! Quelles sont ses limitations ou ses avantages ?
Nous nous sommes alors très rapidement rendu compte que l’un des problèmes principaux auquel fait face l’hydrogène en temps que source d’énergie reste son transport. L’hydrogène étant extrêmement léger et peu dense aux conditions standard de pression et température, il est nécessaire de le compresser à plusieurs centaines de bars. Certaines sociétés telles que McPhy proposent déjà des bonbonnes d’H2 sous pression de 300 ou 700 bars. Mais, tout système de pressurisation est basé sur des compresseurs énergivores et peu adaptés à grande échelle. Échelle qui sous condition d’une acceptation comme stockage énergétique principal deviendra réalité. Nous avons donc décidé de réfléchir à un moyen alternatif de pressurisation, conditionnement et éventuellement production d’H2. L’HCP (Hydrogen Compression Project) était né.
Vous verrez par la suite que ce projet reste au niveau des compétences de deux élèves de seconde y réfléchissant sur leur temps libre. Il reste néanmoins pour nous crucial dans l’évolution de nos réflexions.
L’architecture
Principe de fonctionnement de la compression
L’objectif premier de l’HCP est la compression et “l’embouteillage” de l’Hydrogène de manière rapide et économiquement viable. Nous avons donc tout simplement commencé à chercher où une telle contrainte technique peut être naturellement présente. La réponse est plutôt simple : au fond des mers.
Un rappel s’impose néanmoins. Nous étions à l’époque en classe de seconde. Les dérivées, intégrales (de surfaces) et autres outils mathématiques nous étaient encore inconnus à l’époque ! Le simple fait de calculer la pression sous-marine sous une hauteur d’eau donnée était un défi en soi ! Nous avons donc dû commencer avec l’approximation souvent faite que tous les 10 mètres de profondeur, la pression est augmentée de 1bar. Pour atteindre les 700 bars initialement voulus, il faudrait donc atteindre les 7000m de profondeur. Par chance, des profondeurs équivalentes sont facilement atteintes un peu partout sur Terre. Et des profondeurs entre 6000 et 8000 mètres de fond sont accessibles de manière assez homogène autour du globe.
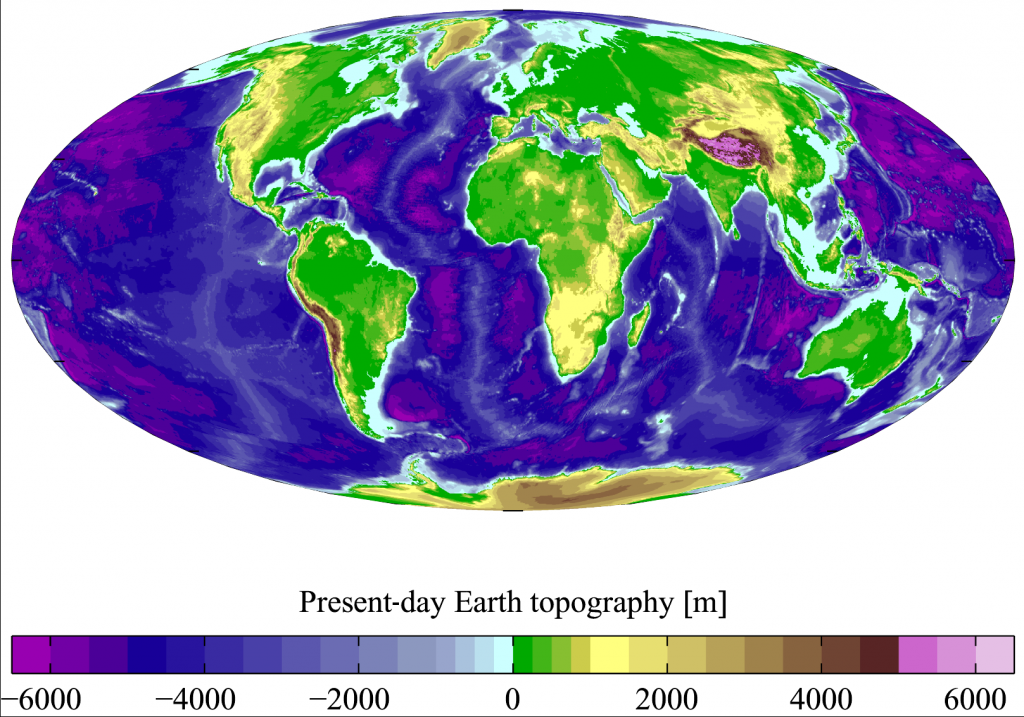
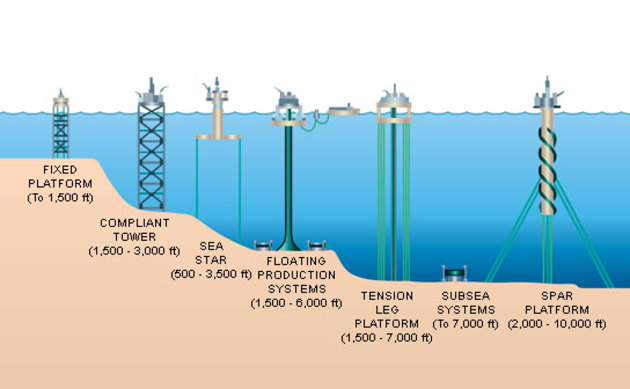
Le défi restait de trouver un moyen de descendre à de telles profondeurs tout en prenant en compte les conditions climatiques difficiles, l’ancrage au fond océanique complexe et un coût devant rester compétitif. La solution la plus simple apparaissant face à ces contraintes était la réutilisation des technologies préexistantes autour du forage des énergies fossiles. Nombre de plateformes pétrolières sont déjà en utilisation. Certes, la plupart sont en eaux peu profondes, car plus rentables et moins chères à construire. Mais, des technologies de construction en eaux profondes ont été mises au point. Notamment, les plateformes de type Spar (voir ci-contre) sont particulièrement adaptées à notre situation. De par leur tube de stabilisation profond, elles sont peu sensibles à la houle et leur installation dans des eaux de plusieurs milliers de mètres n’est conditionnée qu’à leur encrage au fond sous marin.
La limite actuelle de ces installations est d’environ 2500 mètres (cf. la plateforme Perdido). Mais, cette limite est majoritairement en place pour des questions de stabilité du forage et du tube de remontée. Problématique n’existant pas dans le cas d’une compression avec descente en eau profonde.
Dans notre cas, nous avons donc opté pour associer les plateformes de type Spar à un mécanisme de citerne géante. Cette dernière emmagasine une multitude de bonbonnes, toutes prêtes à être remplies. Ainsi, la cuve principale serait certes chère à construire (sa surface importante rend sa construction compliquée), mais elle serait réutilisable à la différence des bonbonnes individuelles qu’elle contient, diminuant ainsi son coût à l’utilisation. La pression sous-marine exercée sur ” l’embout ” de cette cuve principale serait alors répartie dans les bonbonnes par un système hydraulique.
Cette cuve serait descendue et remontée sur la plateforme Spar de manière mécanique et les bonbonnes seraient bloquées une fois leur pression interne désirée atteinte.
Le problème de l’approvisionnement
Un défi est cependant apparu évident à nos yeux. L’Hydrogène devait être approvisionné en pleine mer. Ce qui, dans des conditions de production à grande échelle demande deux choses. Soit un approvisionnement d’Hydrogène peu compressé par tanker géant (principe existant déjà pour le butane), soit une fabrication d’hydrogène sur place.
Cette dernière option est arrivée comme une évidence. Les défis pour la mettre en oeuvre sont cependant nombreux. Dans un premier temps, une désalinisation de l’eau doit être effectuée. S’en suit une Électrolyse de l’eau au sein de la station. Et enfin un envoi direct vers les circuits de compression.
Bien sûr, en établissant ce modèle, nous avons également remarqué ses limites.
– la désalinisation et l’électrolyse de l’eau sont des processus énergivores. Il faut donc avoir à disposition une source d’énergie électrique suffisante.
– les électrodes des électrolyseurs sont extrêmement sensibles aux impuretés de l’eau transformée, et ont une dégradation rapide.
Pour pallier le premier point, nous avons jugé bon d’utiliser le fait qu’en milieu océanique, les courants marins et les vents violents constituent de formidables sources d’énergie. Des hydroliennes ont donc été ajoutées aux rendus. A l’époque, nous avons réalisé des estimations de puissances nécessaires par rapport aux débits de production d’H2 que nous estimions. Malheureusement, ces calculs ont depuis disparu.
Les limites de nos connaissances scientifiques
Nous n’avions pas encore le bagage scientifique nécessaire pour remarquer certaines problématiques. Notamment, que la forte augmentation en densité de l’H2 ne permettrait pas une compression d’une quantité suffisante d’H2, puisque trop peu serait stocké dans la cuve principale au départ de la plongée. Nombre de considérations industrielles quant à la longévité de certains équipements dans des conditions extrêmes manquaient encore à notre analyse. De nombreuses simulations poussées auraient dû être réalisées. Et, plus important encore, il existe maintenant des compresseurs mécaniques d’une grande efficacité permettant de paliers beaucoup plus simplement aux défis lancés par l’HCP.
Cependant, ce projet constituait notre toute première approche à une réflexion poussée (au niveau de nos compétences de l’époque). Il a permis d’éveiller notre intérêt sur le potentiel de l’Hydrogène comme moyen de stockage d’énergie dans un futur proche. Ce projet nous a également permis de nous exercer à la modélisation 3D sous SolidWorks. Nous avons donc produit plusieurs rendus 3D des bonbonnes (avec pas de vis) et de la plateforme telle que nous l’imaginions à l’époque.
Vues des modèles SolidWorks réalisés dans le cadre de ce projet :
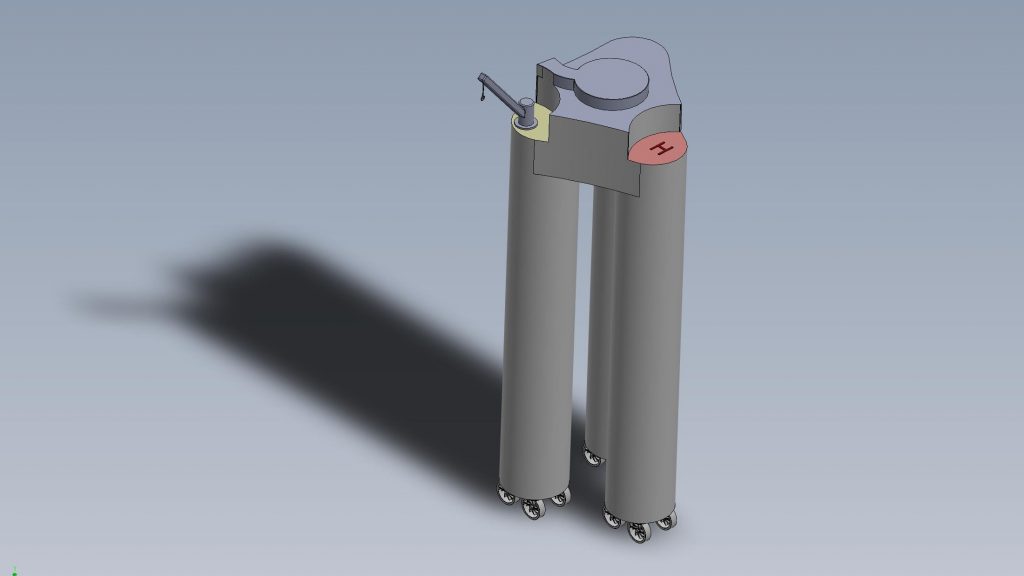
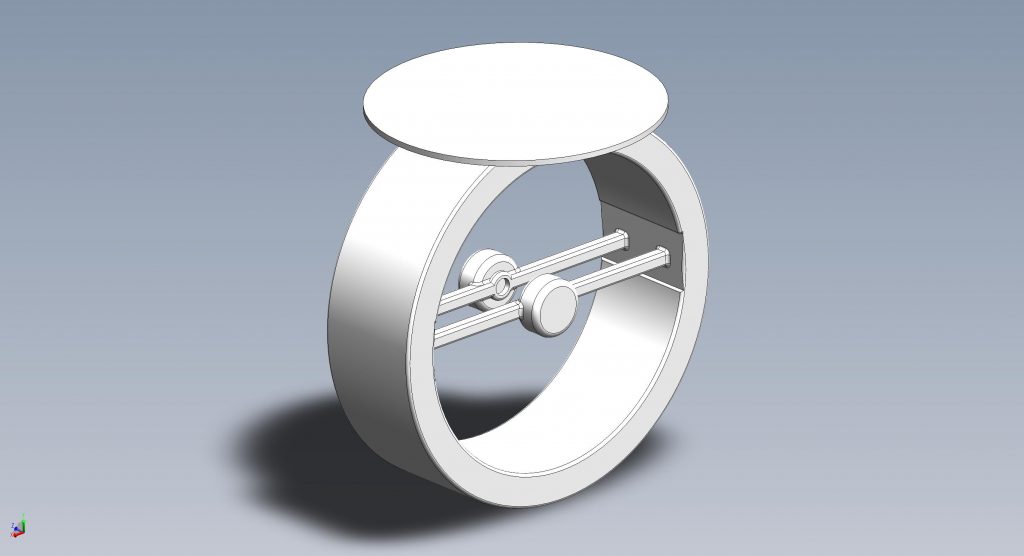
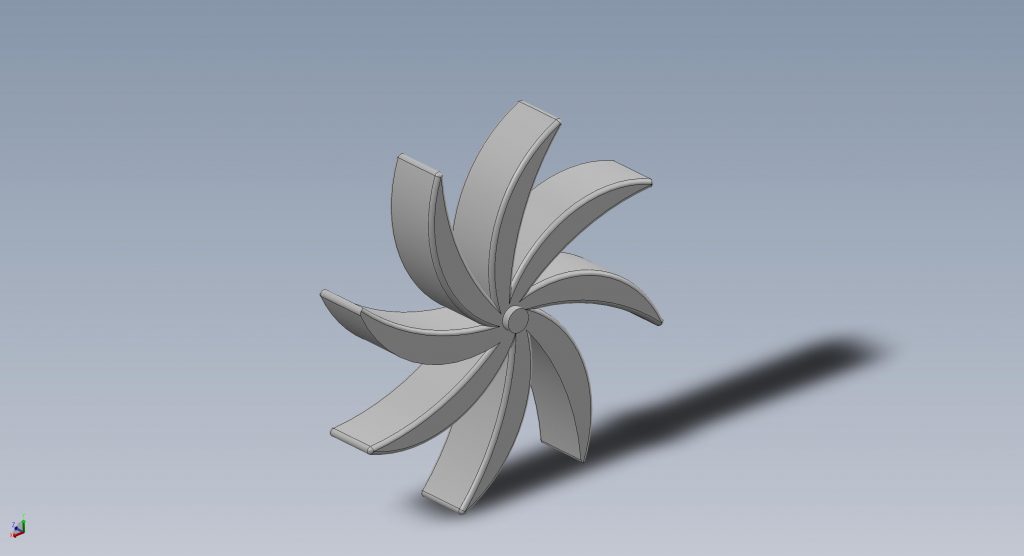
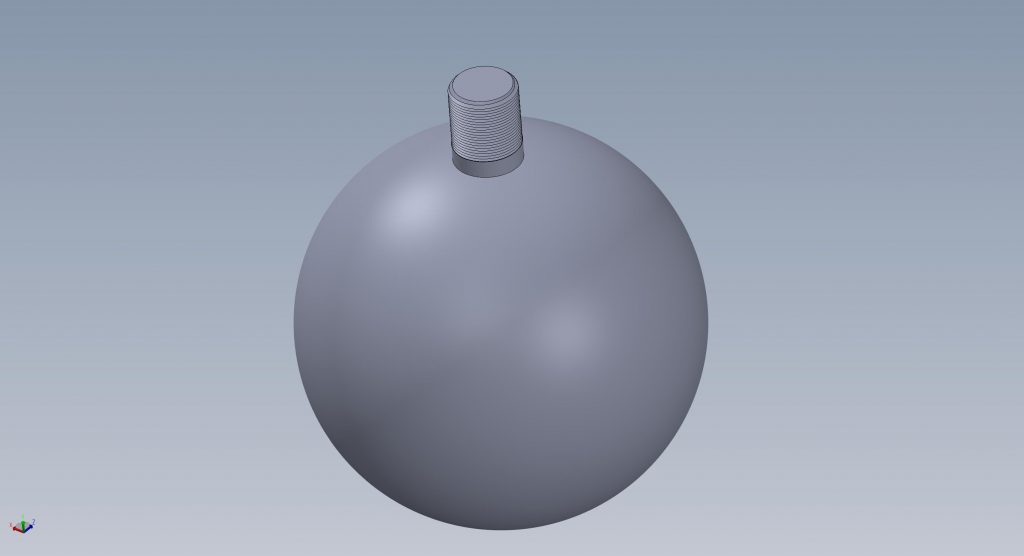
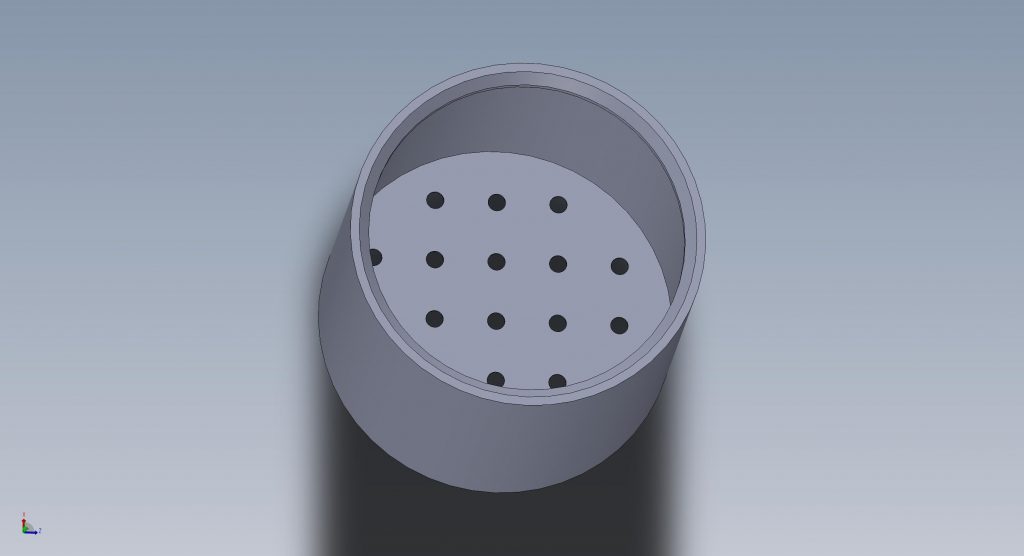
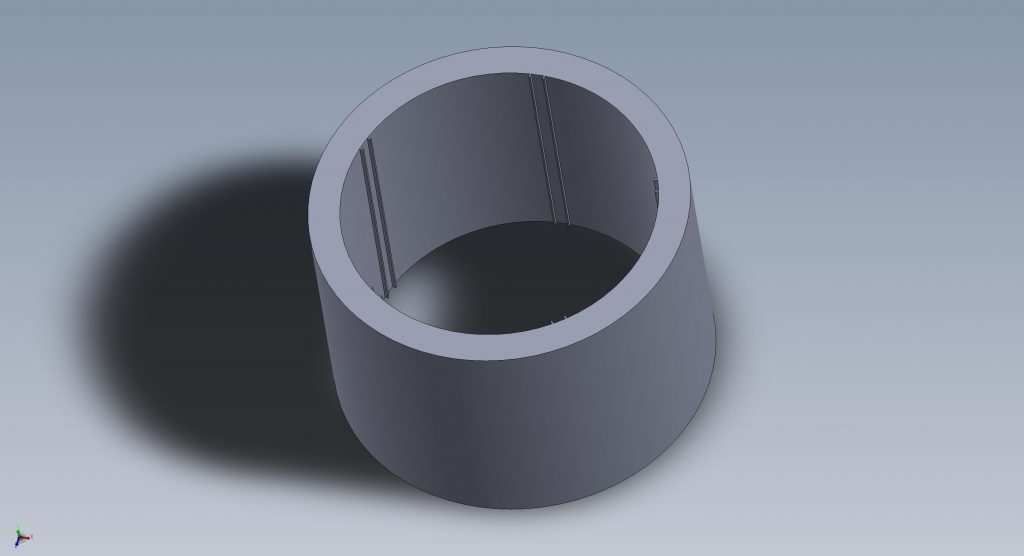
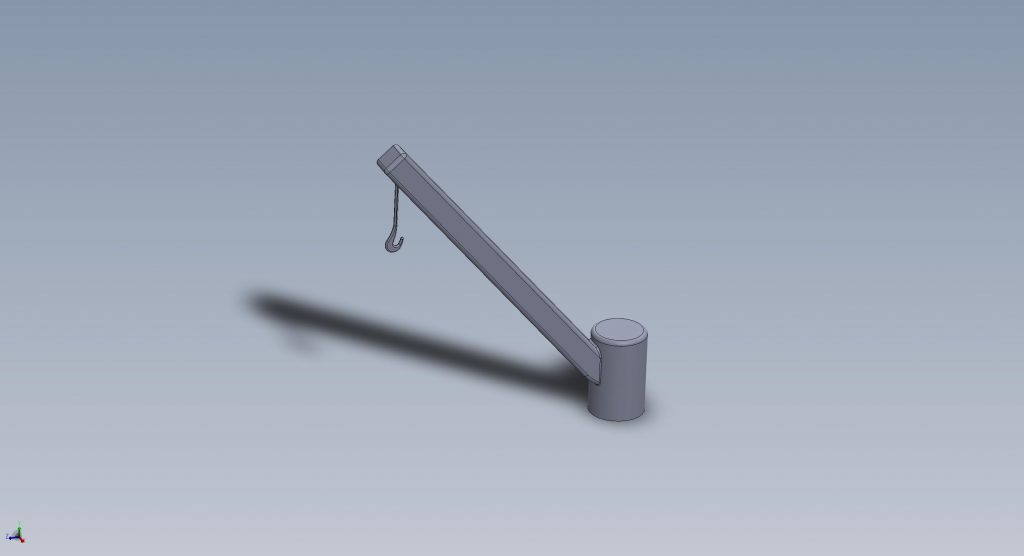
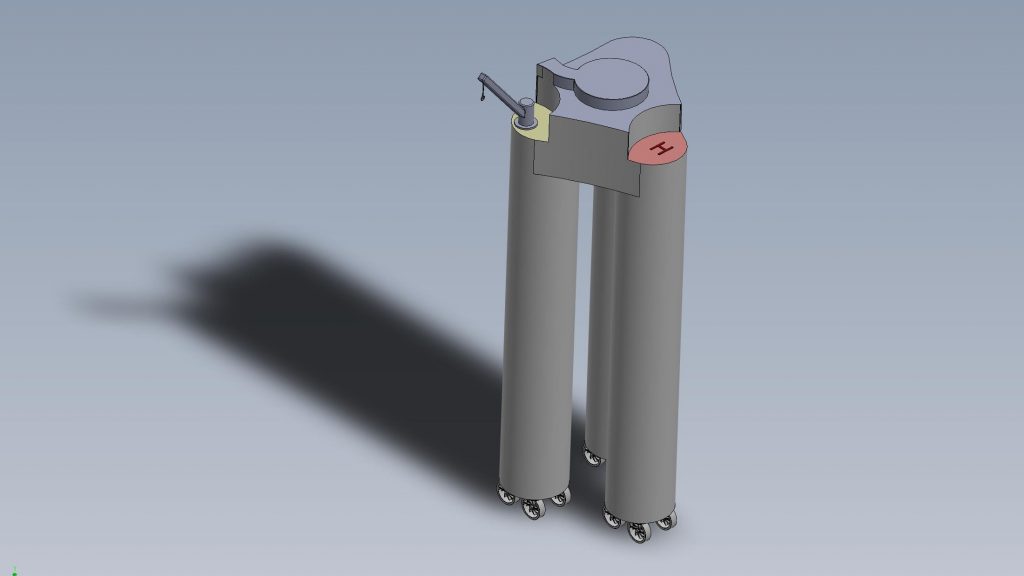
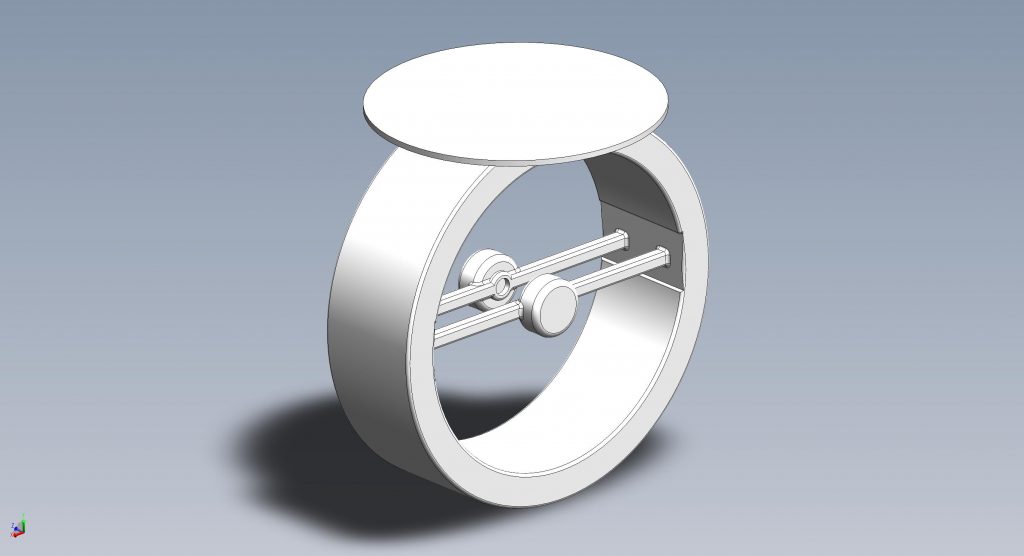
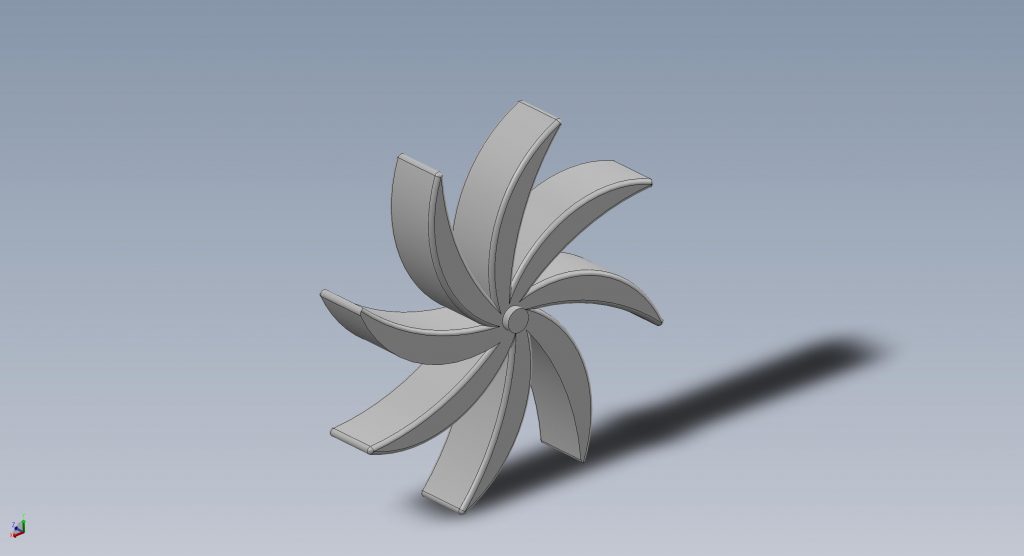
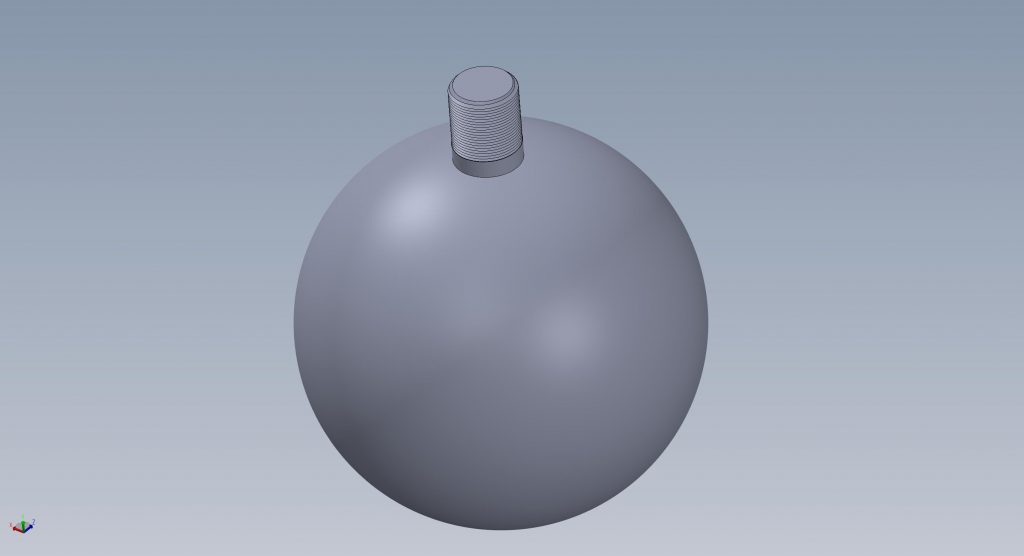
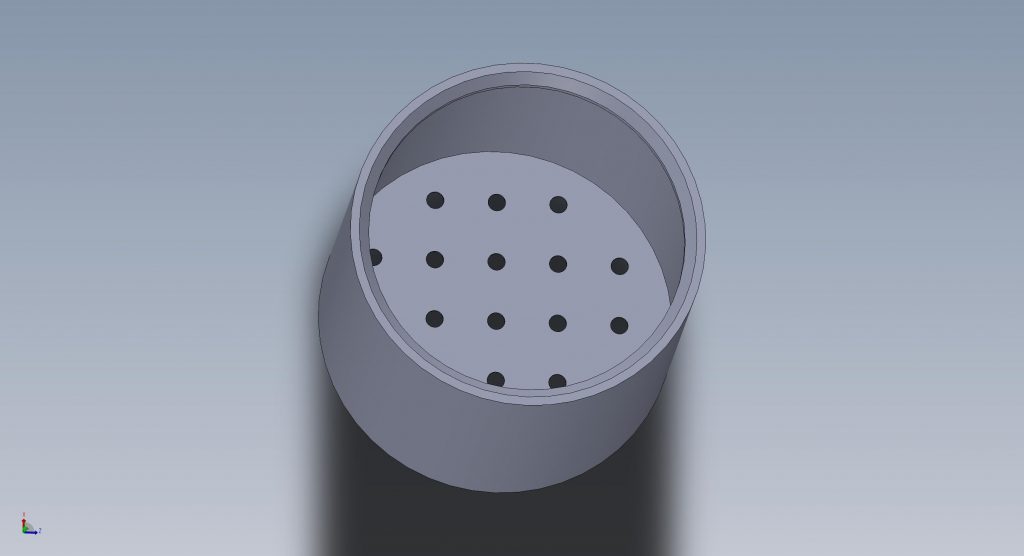
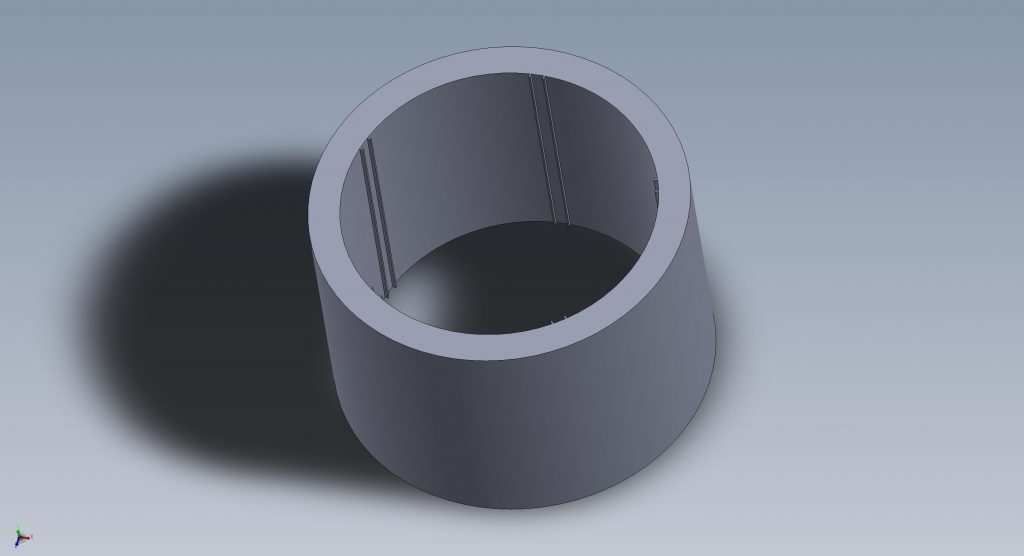
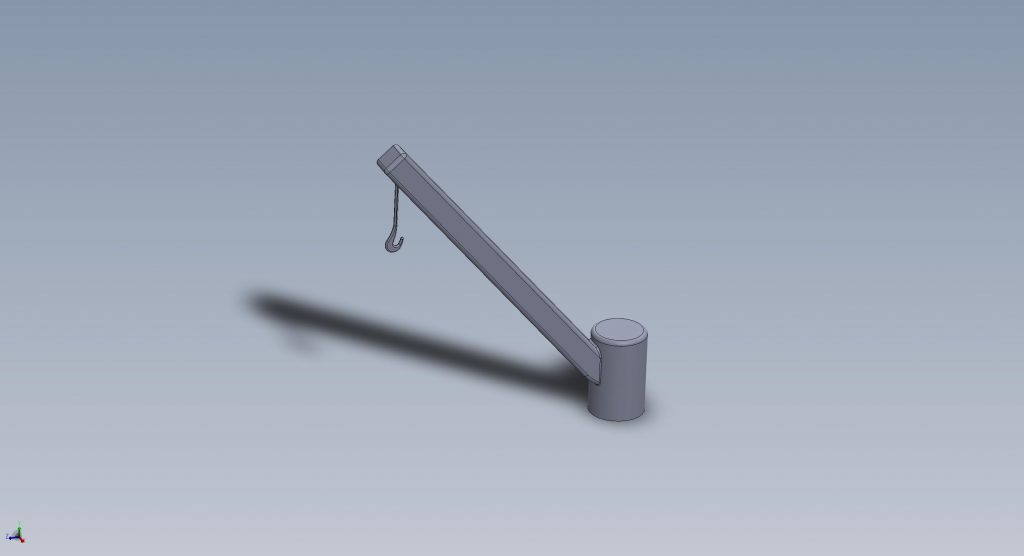